As published in Plastics Machinery Magazine, February 2020
Feb 1st, 2020
BOLE introduced several features on its DK series of injection molding machines, which are fully hydraulic two-platen machines with clamping forces ranging from 585 tons to 7,644 tons. Sixteen models are available in the DK series and each one can be equipped with three different screw diameters, according to Alfred Rak, president and CEO of BOLE.
Updated DK-series machine features include electrically actuated split tie-bar nuts, tie bars that are made of forged steel, a new screw tooth design on the tie bar and linear guide rails.
“The electrically actuated split tie bar nuts improve cycle times 15 percent to 20 percent compared to other hydraulic machines equipped with a classic closing mechanism,” Rak said. “I am not aware of any other major IMM manufacturers that offer this. It is a unique feature and selling proposition to BOLE in the industry.”
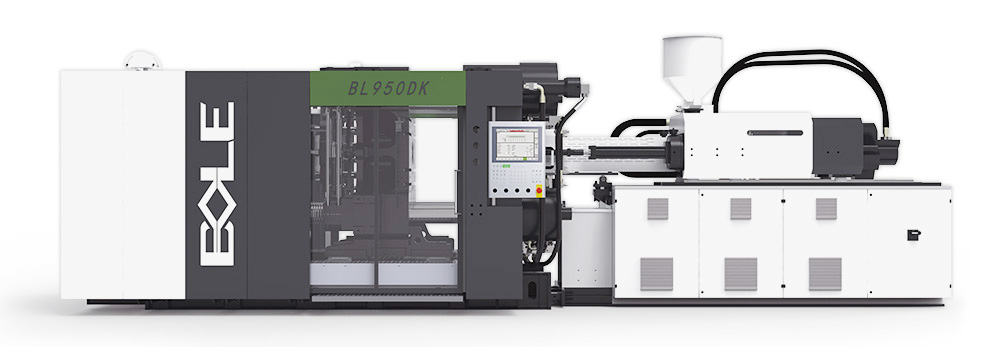
BOLE's DK series of injection molding machines has been updated to facilitate a smoother operation.
BOLE Machinery Inc.
The tie bars on all DK-series injection molding machines are now made of forged steel, which is stronger than the tie bars on previous DK models that were made of machined steel.
“The forged steel tie bar has a 7.5 times safety factor built in to hold the pressure of the IMM,” Rak said. “We are almost guaranteeing that there will be no cracked or broken tie bars.”
In addition to the forged steel, a new screw tooth design on the tie bar contributes to stronger, smoother operations, he said.
“The tie bar now has a progressive screw tooth design for even stress on each of the teeth,” Rak said. “The tie bar has grooves where the tie-bar lock engages. They have a variable tooth spacing for even force application.” Previously, teeth were equally spaced, which did not distribute force as evenly, he said.
“The variable tooth spacing means the force is evenly spread out. The tie bar engages for even force application,” Rak said. “The distance from one groove to the other grooves is not even. The grooves that are further away from the platen [have] a smaller distance, rather than those that are closer. The reason is the stress and the force from the most remote grooves looking from the platen toward the end of the tie bar have to [absorb] a larger stress than those that are closer to the platen. It is patented and unique.”
All of BOLE’s DK series injection molding machines now use linear guide rails, which offer smoother operation. “The linear guide rails are instead of regular flat steel-on-steel gliding shoes that were not linear,” Rak said.
At K 2019, BOLE exhibited an updated 520 DK machine, which made an under-the-hood cover part for the automotive industry. The redesigned DK series is available in North America. Bole plans an open house at its Stow, Ohio, headquarters this summer to showcase the injection molding machines in the series, including the BL950 DK, which the company is targeting to automotive customers and others with larger molds.
Looking for more information pertaining to this article and our premiere injection molding machinery? Please contact BOLE Machinery and we will be delighted to answer your questions. You may also contact our Dealers nearest you.
The world’s well-known brands trust Bole
![]() | ![]() | ![]() | ![]() | ![]() |
Copyright 2021 BOLE America
THE MANUFACTURER RESERVES THE RIGHT TO MAKE CHANGES AND/OR IMPROVEMENTS IN DESIGNS & DIMENSIONS WITHOUT PRIOR NOTICE AND WITHOUT INCURRING ANY OBLIGATION.